WHILE CENTRIFUGAL PUMPS HAVE A SIZEABLE INSTALLED BASE IN THIS INDUSTRY, MANY BENEFITS CAN BE REALIZED IF THE OPERATOR CONSIDERS AN ALTERNATIVE TECHNOLOGY
By Josh Pepper and Michael Moore
Introduction
The universe of liquid-storage terminals – whether they handle such varying commodities as petroleum products, alternative fuels, mainstream or niche chemicals – continues to expand. For proof, all one needs to do is consult the database of independent and commercial tank-storage facilities that can be found at
tankterminals.com.
There, the viewer will see that as of early March 2017, total terminal storage capacity stood at 953,258,444 m3 with 4,604 tank-storage facilities covering a network that includes 2,276 ports or cities and 161 countries. For comparison, those figures more than double the total storage capacity (423,575,602 m3 ) and terminal facilities (2,150) that existed in 2009 and represent significant increases in the number of ports/cities (1,249) and countries (132) that harbored tank-storage facilities eight years ago.
Growing long-term demand worldwide has driven this rapid and consistent expansion. Because of this, pumping technologies that have been proven to help maximize safety, production efficiency, uptime performance, delivery-system accuracy and environmental compliance are increasingly important to operators for both new and existing facilities. In other words, as the liquid-terminal market continues its upward trend, from the largest port terminal to the smallest regional bulk station, petroleum tank-truck or chemical transport, operators must employ pumping technologies that are ideally suited for numerous fluid-handling characteristics and applications.
Traditionally, centrifugal pumps have been a go-to technology for liquid-terminal operators, with some estimates indicating that centrifugal pumps are utilized at nearly 75% of these sites. This white paper, however, will illustrate how a different technology – positive displacement twin- and triple-screw pumps – can oftentimes be a more versatile, reliable and efficient choice than centrifugal pumps in critical fluid-handling operations in the wide-ranging and ever-expanding liquid-terminal industry.
The Challenge
The most obvious challenge – and perhaps the toughest to surmount – in making screw pumps more prevalent in liquid-terminal applications is convincing the industry’s operators to move away from a technology that has become defined as the best one for a variety of unique fluid-handling tasks. Generally speaking, the bulk of the fluids that are handled at liquid terminals must be transferred at very high flow rates and volumes, which hits the operational sweet spot of centrifugal pumps.
Because of the success of centrifugal pumps in these types of operations, the fluid-transfer systems at liquid terminals have been designed around the pumping technology, rather than the other way around. This means that engineers are familiar with centrifugal pumps and then attempt to work within their operational limits. They know how centrifugal pumps operate, know their benefits and are confident that they are still the best technology for all of their many fluid-transfer needs.
To illustrate this mindset, in some cases a design engineer – instead of considering an alternative pumping technology – will blend or heat the liquid that needs to be transferred as a way to manipulate the process and get the viscosity of the fluid down to less than 300 cSt, which makes it easier for the centrifugal pump to transfer the fluid. What they are doing in this instance is reconditioning the fluid to fit the pumping technology – irrespective of the cost impact.
In other words, when measures like this are taken to satisfy the needs of the pump, the popularity of centrifugal pumps in liquid-terminal fluid-transfer applications becomes something of a self-fulfilling prophecy.
Despite the ability to recondition the fluid to meet the operational needs of the centrifugal pump, operators must still take care to ensure that the centrifugal pump is operating on what is known as its “Best Efficiency Point,” or BEP. The BEP is the point where the centrifugal pump is working at its highest level of efficiency. Centrifugal pumps seldom operate at their exact BEP because pristine pumping conditions are rarely realized, but a centrifugal pump that is able to function in a window between 80% and 110% of its BEP is said to be functioning adequately.
However, when the operation of the pump moves too far off its BEP uneven pressure will be applied to the impeller, which can result in increased radial thrust that will cause the pump’s shaft to “deflect.” When this deflection occurs, higher loads will be placed on the bearings and mechanical seal, which can lead to damage to the pump’s casing, back plate and impeller. Ensuring operation at the BEP can be a time-intensive task as the pump must be monitored constantly and adjusted, which costs time and money.
Regardless of the flow rates and volumes that must be achieved, there are other considerations the liquid-terminal operator must contemplate before deciding on the best pump technology, including:
? Varying loading requirements and different flow rates that need to be delivered to varied locations throughout the day
? Intermittent service that requires quick, multiple starts with minimal line priming
? Varied shipping media with differing fluid-handling characteristics
? Effective stripping of transport and storage vessels to maximize deliverable working volume while managing gas entrainment without the threat of pump shutdown due to vapor locking
? Meeting strict cycle times regarding incoming and outgoing shipments, with any delays or shutdowns resulting in the incurrence of prohibitive charges or financial penalties that can reduce the terminal’s profitability
? Level of risk for an explosion due to static charge buildup during filling cycles
The Solution
As mentioned, the solution to the operational disadvantages of centrifugal pumps can be positive displacement (PD) screw pumps. The difficulty in expanding the penetration of screw pumps in liquid-terminal settings is not only overcoming the strong customer familiarity with centrifugal pumps, as evidenced by their sizeable installed base, but in getting design engineers to acknowledge or even become aware that there are alternatives like screw pumps.
Simply put, many engineers are not taught about screw pumps in their studies, and many who are aware of them have a preconceived notion of their shortcomings, or that they are nothing more than lube pumps capable of handing only low flow rates. In reality, today’s screw pumps have experienced remarkable advancements in terms of the flow rates that they can handle, with flow ranges from 220 gpm (833 L/min) to 11,000 gpm (41,635 L/min) not uncommon.
In truth, the design of PD screw pumps makes them capable of handling various liquids – even those with higher viscosities that are common commodities in many liquid terminals. The operating principle sees opposed screws engaged to form a sealed cavity with the surrounding pump casing. As the drive screws turn, the fluid is shifted and steadily and constantly conveyed to the discharge port of the pump, which creates a volumetrically consistent flow rate regardless of the pumping pressure.
The list of benefits provided by screw-pump technology in oil-and-gas fluid-handling applications is a long and impressive one:
? Ability to handle a wide range of flows, pressures, liquid types and viscosities without the need to manipulate a BEP position
? Constant flow, even in the presence of varying system backpressures due to viscosity changes
? Elimination of the need to pre-heat fluids as the technology can readily handle high-viscosity fluids without sacrificing performance
? Can accommodate significant turndown ratios when controlled by an adjustable-speed drive, allowing for a wider flow range without wasteful recycling
? Good suction-lift capabilities that can maximize lines-tripping operations while being able to tolerate the intake of entrained air and other gases without vapor locking
? High volumetric and overall operating efficiencies, resulting in reduced operational costs
? Can deliver high and constant flow rates even when exposed to upstream and downstream pressure fluctuations, ensuring consistent loading and unloading times
? Low internal velocities
? Low mechanical vibration lengthens service life
? Intrinsically smooth and quiet operation
? Extremely low pulsation reduces stress and prolongs life of associated fluid-transfer components (piping, hoses, etc.)
Realizing the operational advantages that can be achieved when using screw pumps in liquid-terminal fluid-transfer applications, Blackmer
?, Grand Rapids, MI, USA, a leading provider of pumps and compressors for industrial use, and a product brand of PSG
?, Oakbrook Terrace, IL, USA, a Dover company, has developed the S Series Screw Pump product line.
Specifically, Blackmer recommends two of its S Series pump models –Twin Screw With Timing Gear (WTG) and Triple Screw – for liquid-terminal fluid-transfer activities.
The Twin Screw (WTG) pumps have been designed with external bearings and a timing-gear transmission, which produces double-suction, self-priming operation with no metal-to-metal contact between the pump’s internal components. This design helps the Twin Screw (WTG) pump achieve the highest flow rates of any rotary PD pump, even at varying backpressures and viscosity levels. In fact, the deliverable flow rate of a PD screw pump, unlike a centrifugal pump, actually increases as the fluid’s viscosity increases. These design characteristics also make screw pumps suitable for all types of transfer applications, including low- or high-viscosity, lubricating or non-lubricating, neutral or aggressive, and clean or contaminated fluids.
The Triple Screw pumps are made to handle clean lubricating fluids without solid content across a wide range of viscosities, temperatures and pressures. They are designed with a male drive spindle, two female secondary spindles and a case that contains the screws, which allows the fluid to move smoothly and continuously in an axial direction from suction to discharge. This method of operation delivers smooth, constant product flow with low noise and high levels of energy efficiency.
Both models feature no metal-to-metal internal contact, with optional double mechanical seals available as a way to eliminate an ignition source and to safeguard against process-fluid discharges. The result is a safer pump for site personnel, the terminal, surrounding communities and the environment.
Conclusion
As the tank-storage universe continues to grow, a pumping technology that offers numerous and significant advantages in terms of reliability, consistency, versatility and safety stands poised to grow along with it. While screw pumps may have a higher purchase price than centrifugal pumps, it’s best to remember the old bromide that “buying cheap just means you’ll have to buy it again,” and that their total cost of ownership will be lower as time and money won’t be needed for BEP monitoring and adjustments. Besides, the main operational advantages that screw pumps have – the ability to handle a wider window of fluid viscosities at higher rates and pressures, lower energy consumption and no BEP to contend with – leave them poised to become a more efficient, reliable and versatile alternative to centrifugal pumps in critical liquid-terminal fluid-handling applications.
About the Authors:
Josh Pepper is the Global Product Manager – Screw Pumps for Blackmer
?, Grand Rapids, MI, USA, and can be reached at (616) 248-9235 or
josh.pepper@psgdover.com. Michael Moore is Blackmer’s Senior Director, Business Development – Screw Pumps and can be reached at (519) 802-2106 or
michael.moore@psgdover.com. For more information on Blackmer’s full line of pumps and compressors, please go to
blackmer.com or call (616) 241-1611. Blackmer is a product brand of PSG
?, a Dover company, Oakbrook Terrace, IL, USA. PSG is comprised of several of the world’s leading pump brands, including Abaque
?, Almatec
?, Blackmer
?, Ebsray
?, EnviroGear
?, Griswold
?, Mouvex
?, Neptune
?, Quattroflow
?, RedScrew
? and Wilden
?. You can find more information about PSG at
psgdover.com.
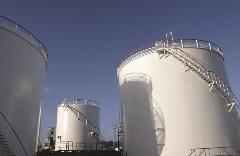
Centrifugal pumps have gained acceptance as a go-to technology for critical fluid-handling applications at liquid terminals. In reality, a better alternative may be the positive displacement screw pump, with Blackmer
? offering its Twin Screw With Timing Gear (WTG) and Triple Screw models as a way for terminal operators to maximize their ability to handle a wider array of fluids at higher viscosities, flow rates and pressures with overall lower total cost of ownership.
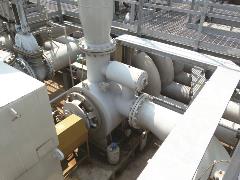
Twin Screw WTG and Triple Screw Pump models from Blackmer
? excel in liquid-terminal fluid-handling applications because they can manage a wide range of flows, pressures, viscosities and liquid types and still provide the constant transfer rates that are critical in these circumstances.
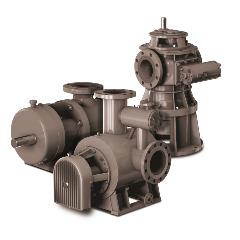
Realizing the many different types and volumes of fluids that must be handled at high flow rates in liquid terminals, Blackmer offers a complete family of highly efficient and versatile twin and triple screw pumps.