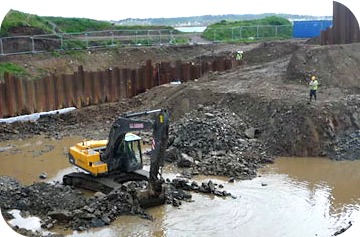
Dewatering, or the removal of water, is a common application for AODD pumps. Regardless of the industry or location in the plant water can accumulate in a variety of areas.
Construction sites can readily accumulate water as they are outside and exposed to the elements. Rain can easily accumulate in a variety of areas and needs to be removed prior to the continuation of work.
Similarly, any loading dock without proper drainage would need to be cleared of water after a heavy rain.
Sumps are commonly found inside and outside manufacturing locations and are purposely installed so that water and other liquid wastes accumulate in a known area. Outside in particular one may find sumps installed in order to prevent water runoff into the surrounding area.
Additionally, during Mining and Tunneling, ground water often accumulates and needs to be removed.
All of the above scenarios pose essentially the same problem. Water accumulated in a set area and must be removed. Because the area of water accumulation is often open, solids and other abrasives are present. Sumps can often contain rocks, metal shavings and other such debris which can pose a problem to water removal.
Water removal is well suited to AODD pumps due to several essential features. AODD pumps are self-priming. All-Flo’s 2 inch model can prime itself up to 24.4 ft. In practice this is very useful as an operator can often drop a hose into a “water hole” and start dewatering immediately.
Caution must be taken to avoid damage to the diaphragms due to the presence of debris in the water. Two practical steps can be taken to mitigate this risk. Firstly, it is common to install a strainer to prevent very large debris from entering the pump. This strainer however does not prevent small debris from entering the pump and causes damage. Secondly, Thermoplastic Diaphragms should be used instead of rubber diaphragms whenever possible. Historically a common diaphragm used for dewatering was Buna-N or Nitrile. A good alternative to this material is the thermoplactic elastomer (TPE) Geolast?. TPEs’ typically have twice the life of their rubber counterpart and are an excellent material when handling abrasives. In many cases where small debris may puncture a rubber diaphragm, a Geolast? would come through unscathed.